
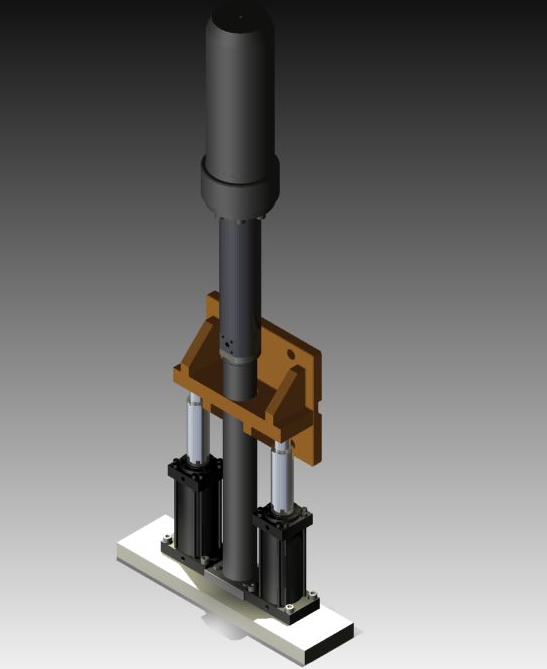
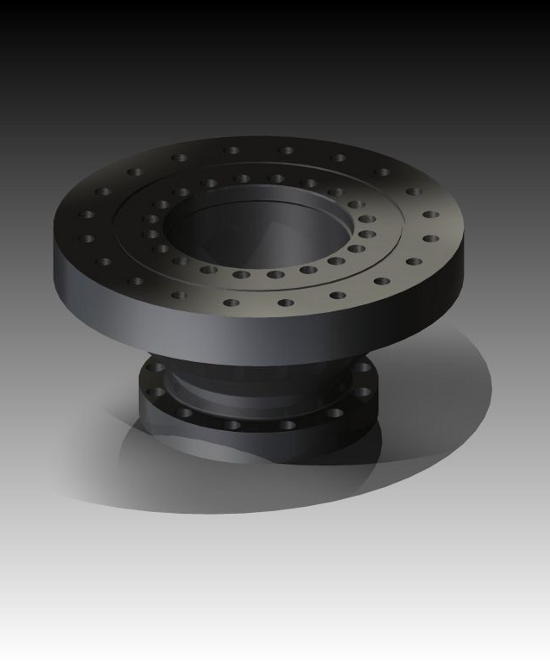
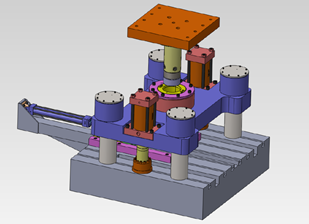
DESIGN AND BUILD OF CUSTOM PRESSES
We design and build new presses for specialty applications up to 500 tons. By utilizing our repair and reconditioning experience from a variety of industries and applications, we are uniquely positioned to apply this experience to design and build new presses that are specifically targeted to your molding, forming or stamping applications. We have designed and built presses in size from 12 – 350 tons for a variety of applications. We also offer specification development for customers who wish to secure quotations from other press manufactures.
AUTOMATED HANDLING AND SECONDARY OPERATIONS
We supply automatic press loading and unloading systems designed to remove labor from the molding or forming operations. We also supply automatic material slitters with incorporated scale tables to automate the charge preparation. Our secondary operation designs include drilling, routing and bonding operations to provide a complete finished product. These systems can be designed with automatic handling in a complete cell or hand load for lower volume manufacturing. Each work cell features long proven hardware and part nesting techniques for a repeatable finished product. We also design universal machining centers that provide a flexible work cell using water jet technology or multiple head tool changing systems for routing and drilling operations. From a simple deflash table to a complete product assembly line, we can meet your material handling and secondary operation needs.
PRESS AND UTILITY CONDITION ASSESSMENTS AND REVIEWS
Often the first step with a new client is to establish a baseline on the condition of the existing equipment and the state of the support equipment and preventative maintenance effectiveness. We utilize our experience to develop a custom designed program to determine the overall condition of your facility and/or equipment. We also utilize our Computerized Press Monitoring Equipment to assess the specific condition and actual performance of your equipment both in production and off line to get a full assessment of the actual condition.
MOLD AND DIE DESIGN
We offer a full line of mold design services for the thermoset industry. Using the experience gained from our process improvement services as well as utilizing our many years experience allows us to design molds that contain the very latest in compression molding technology. Our designs feature heavy duty heal blocks, combination standard ejection and air poppet ejection. Heating/cooling circuits are designed to optimize heat transfer to the mold surface and ported to allow adjustable heal blocks. Advanced features such as vacuum, cure sensing and in-mold thermocouples is always an option depending on the application. Cores and in-mold cams as used where required dependent on the part configured. In short, we can design the mold for your product.
We apply the same technology and approach in the design of specialty die applications. We start by examining the requirements of the finished product, understand the limitations of the press and process equipment and then develop a die design that provides value, quality and reliability required for the particular application. Past applications have included titanium compaction, steel forming and PET plastics processes.
FACILITY AND UTILITY DESIGN
We offer a complete line of facility design services. These design services include process layout and product flow as well as building construction specifications. We can also specify and layout facility support systems such as electrical power distribution, compressed air, ventilation, steam supply systems and dust collection. Mold/die repair and handling systems can also be incorporated into the complete facility design.
PROJECT MANAGEMENT AND SITE SUPERVISION
Every project or service we offer comes complete with professional project management and skilled on-site supervision. Each stage of the project is planned and published using Microsoft Project™ to make sure everyone involved in the project is up to date on the progress of the project. Our site supervisors are in charge of all site activities with a special focus on safety at the worksite. They are also in constant communication with our engineering and rebuild centers to make sure the project stays on time and on budget. As issues arise throughout the course of the project not covered by the primary contract, we utilize our “Open Issues” publication to track these additional tasks or discuss issues and their resolution. Engineering Change Orders (ECO) are used to track any scope changes and receive client approval.
PRODUCT DESIGN
We are a full service product design firm specializing in the design of plastic products. Our engineers can work either with the molder or the products end user to develop a complete product concept. Multiple component products can include bonding and hardware specifications as well as prime or finish painting specifications. We can take your product from concept to a molded part as a turn key package. With the experience of our engineering staff we can insure manufacturability of the finished product.